CSIRO Develops New Refining Method For Titanium
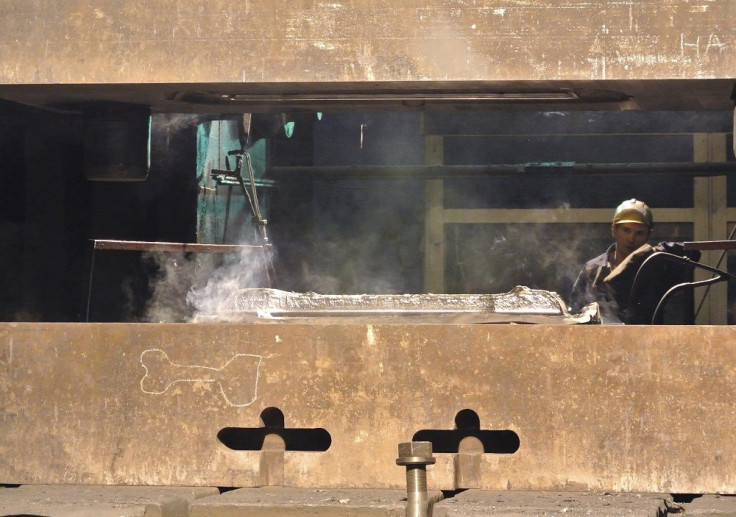
The Commonwealth Scientific and Industrial Research Organisation, or CSIRO, is developing a new method that will minimise the wastes generated from the conventional processing of titanium, while significantly boosting the country's production capacity for the mineral, several sources said. John Barnes, CSIRO's director of high performance metals, told The Age that his team has been developing a chemical process that utilises less energy and reduces waste products than a metallurgical process.
About 95 percent of titanium minerals extracted from ores are used to manufacture titanium dioxide for the pigments industry. The rest is used to create titanium sponge, or metal, which are used in the aerospace or medical segments. The process of converting this small amount, however, is not environmentally sound and hasn't changed much since the 1950s.
"When you're machining away 90 per cent of what you want there's a bit of a perverse relationship," Barnes noted in the report. "The industry average is about 11 to one [raw material versus finished product], so you're wasting well over 90 per cent of what you're buying and it goes back into a recycle stream that doesn't have enough value," added Barnes.
In a separate report by Manufacturers' Monthly, Barnes revealed that his team also aims to manufacture titanium by using additives and through the use of electron beam melting and coldspray technologies. The report stated that CSIRO's Lab 22 was the first "southern hemisphere location" that owns an Arcam machine, which it acquired in 2012. The machine is capable of melting titanium on a powder bed through electron irradiation.
Australia’s current titanium deposits are expected to be depleted in 90 years. Barnes believes that through the development of such titanium processing technologies, the country could make most of its titanium resources for 9,000 years.
The new refining method would also allow Australian producers to process large quantities of titanium and position Australia as a global leader in the sector. Australia is among a small number of titanium producers that are currently innovating in the space. In Chile, White Mountain Titanium Corporation (OTCQB:WMTM), has also developed a similar technology which brings down the cost of converting titanium concentrates into titanium metal, while lessening its impact on the environment.
Called the Chinuka process, the electro-refining technology is capable of producing high-grade titanium metal powder directly from rutile and ilmenite concentrates. White Mountain has already used the technology with success on rutile concentrates it has extracted from its Cerro Blanco project in Santiago, Chile.
The company developed Chinuka in partnership with the University of Cambridge. It has received full patents from the United Kingdom, Russia and China. The process can also be applied to other transition metals such as niobioum and tantalum.
To contact the writer, email: v.hernandez@ibtimes.com.au