Mining Segment Recycles Titanium Scraps To Improve Environment
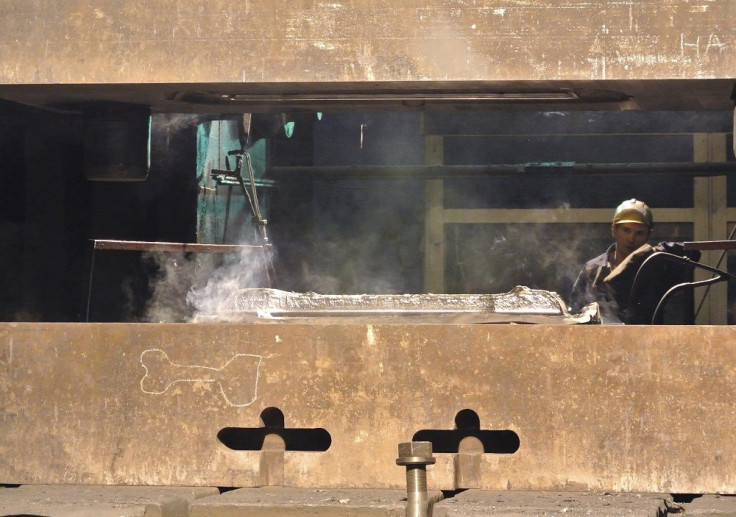
Aircraft engines, surgical implants, paints and pigments—these are just some of the uses of titanium and its alloys. Thanks to titanium's lightweight makeup, anti-corrosive properties and high melting point, it is the metal of choice for a wide variety of applications. In fact, very few other metals can substitute for the properties of titanium.
Because of the high demand for the metal, more and more titanium mining explorations are being developed, especially in sandy areas and dunes that contain heavy concentrations of minerals. One of them is the Cerro Blanco deposit located in the Atacama Region of Chile, which is considered as the driest place on Earth. Developed by White Mountain Titanium Corporation (OTCQB: WMTM), the Cerro Blanco Project has the potential to become one of the largest primary rutile mines in the world at an estimated 112 million tonnes. White Mountain Titanium Corporation is expected to enter production at the end of 2017.
But the large amount of titanium manufactured in different industries also means that there is a huge amount of titanium scrap to recycle. In fact, titanium scrap seems meant to be recycled because of its virtually limitless lifespan. Only around 30 percent of titanium used in manufacturing ends up in the finished product, resulting to a lot of titanium scrap.
One of the biggest sources of titanium and titanium alloy scrap is the aerospace industry. Titanium is recycled from engines and other structural components of airplanes, satellites and space crafts. These scraps can then be turned into surgical joint replacements for medical use, armor plates for military vehicles, and even sports equipment like golf clubs. Over 50 percent of the titanium feedstock for ingot production comes from titanium recycling.
Many businesses are into titanium recycling because of its potential as a renewable resource. Furthermore, recycling titanium has valuable environmental benefits, including less pollution because of the use of less energy in sourcing and producing components from raw materials. More recycled titanium also means that there is a reduced need to dig for virgin materials, hence conserving wildlife habitats as well as protecting the integrity of the soil. Though recycled titanium is less valuable than copper, it has more market value than stainless steel and other ferrous metals.
Recycling process
Titanium recycling basically consists of converting titanium scrap into titanium ingot with or without virgin metal. There are two informal classifications of titanium scrap: it is "new scrap" when it comes from the production and fabrication of titanium components, while it is called "old scrap" when it is recycled from used components like old aircraft parts, heat exchangers, submarine hulls and other titanium industry applications.
One of the most used recycling methods for titanium scrap is the IME recycling process developed by the Process Metallurgy and Metal Recycling of Aachen University in Germany. It is designed to handle 100 percent low-grade titanium scrap feedstock, hence lowering the cost of recycling.
The IME recycling process consists of three main steps: conditioning, vacuum induction melting and vacuum arc remelting. Conditioning reduces impurities in the scrap as well as compacts loose scrap to ensure sufficient energy input during vacuum induction melting.
The next step makes use of a vacuum induction furnace that consists of a vacuum chamber and water-cooled copper coil lined with appropriate refractories. Alternating current powers the conductor, therefore inducing an alternating magnetic flux that leads to an eddy current. This current, in turn, leads to conducive heating of the titanium scrap. Intensive stirring and homogenisation of the melt takes place.
The last step is vacuum arc remelting, which makes use of a vacuum arc furnace composed of a vacuum chamber and water-cooled copper mold. A direct current is applied between electrode and ground plate, causing an electric arc that melts the electrode. Drips then start to form at the bottom of the electrode, accumulating in the mold and forming a new ingot.
Recycling problems
In general, the issue of quality is at the heart of scrap metal recycling, since recycled metals can vary in quality. The produced alloy many not be able to meet current alloy specifications, rendering it less useful than extracted alloys. Furthermore, the recycling process itself emit pollutants when breaking down different products, albeit not as much as the metal extraction and refining processes. The metals recycling industry also creates low-quality, menial jobs, such as sifting through garbage, dealing with toxins from the breakdown process and other manual-intensive labor tasks.
Still, the advantages of titanium metal recycling far outweigh its disadvantages, making it a viable industry for sustainable mining practices.
To contact the writer, email: v.hernandez@ibtimes.com.au