3D printing shapes future of human surgeries
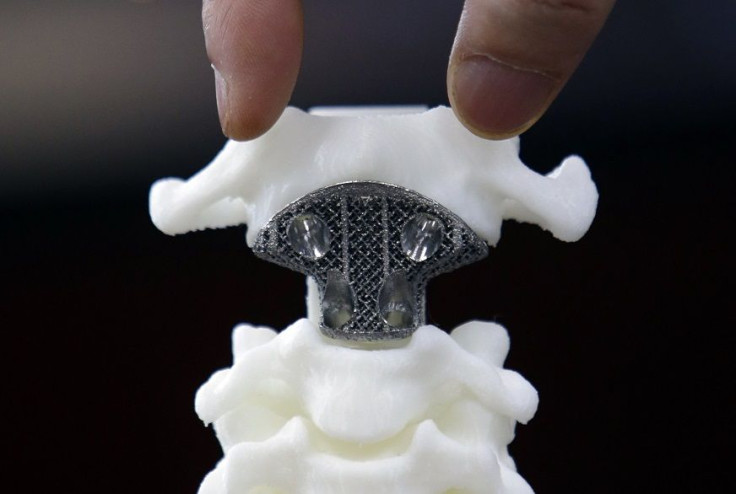
Signaling the latest medical breakthrough that involve three-dimensional printing technology, a six-year old boy with brittle bone disease was able to stand again after undergoing surgery in southern China.
To determine precisely where to make incisions on the bones, doctors used a 3D skeleton model prior to the operation. This pioneering technology lessened surgery time and pain for the patient. The innovative 3D skeleton, made of photosensitive resin, was produced by the Shenzhen Sunshine Laser and Electronics Technology for around 2,000 yuan.
Over the past few years, the concept of 3D printing – an additive manufacturing technique that builds objects layer by layer – has turned from fiction to reality. Known as biofabrication, the process is used by scientists to regrow most types of human tissue using 3D printers. From bionic eyes to limbs, recent clinical breakthroughs have pushed this technology into the mainstream, benefitting patients worldwide.
Australia, which successfully produced an implanted titanium heel and jawbone, has become a leader in the field of biofabrication. Queensland University of Technology, or QUT, has been spearheading research into the area for the past few years. At the helm of the study is Dr Mia Woodruff of the Biomaterials and Tissue Morphology Group at QUT's Institute of Health and Biomedical Innovation. Using a biofabrication machine that imparts thousands of volts and robotic precision, the project could result to print 3D models of specific parts of the body that need to be operated as well as print a scaffold that can be implanted as replacement.
In July 2015, QUT joined forces with three leading research universities in the 3D printing of replacement body parts to provide the world’s first International Master in Biofabrication. Partnering with QUT are the University of Wollongong in Australia, the University Medical Center Utrecht in The Netherlands and the University of Würzburg in Germany. Graduates of the programme will earn a master’s degree from an Australian university and from a European university.
Still in the field of medical studies, a team of experts in Melbourne has developed a 3D-printed anatomy kit to replace cadavers, which are crucial but expensive tools for training doctors.
Monash University, which created the printed body parts, hopes that this will revolutionise medical training around the world and change the future of medical education.
Contact the writer at feedback@ibtimes.com.au or tell us what you think below.