Titanium Is The Metal Of The Future
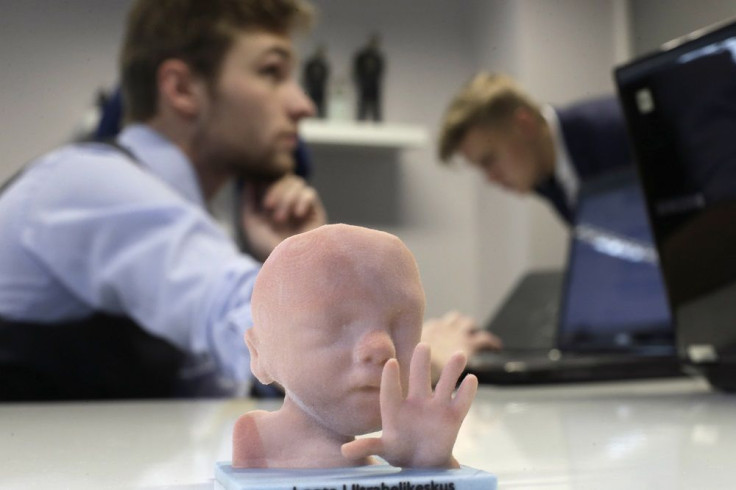
For countless years, titanium has been playing a huge role in the aerospace, medical and architectural industries, thanks to its high strength-to-weight ratio. In fact, it would have been the metal of choice for these industries, had it been cheaper than the more commonly used metals like stainless steel and aluminum. The complicated process of producing titanium through the conventional Kroll system might also be hindering the metal from reaching its full potential. Fortunately, the latest technological developments might actually make titanium the metal of choice in the future.
For one, the Cambridge University's invention of a new process of titanium production is a welcome development in the goal of making titanium cost-effective in mass-produced goods. The process, known as metalysis, bypasses the complex chlorine-based stages used in the Kroll system. Instead, it uses electrolysis to produce titanium powder and other rare metals like tantalum. Aside from making production faster, metalysis also makes titanium cheaper and more accessible to businesses that need it.
Though the process is not yet mainstream, the company behind it, also known as Metalysis, is working on making the process commercially available so that the intricate Kroll system would now become a thing of the past.
Another exciting development for titanium is the increasingly widespread adoption of 3D printing, also known as additive layer manufacturing. It makes use of titanium powder in the process of making three dimensional objects from a digital file. The object is then created by laying down successive layers of material, visible as thinly sliced horizontal cross sections, until the entire object is completed. With titanium powder, the entire product exhibits near perfect sphericity and size uniformity. Furthermore, metalysis-produced titanium powder is significantly lower in cost compared to powder produced through conventional processes.
Titanium producers would be of utmost importance if the metal is to be mass produced at cheaper prices. Foremost among these producers is Australian company Iluka Resources, which is the best known producer of mineral sands like rutile, ilmenite, synthetic rutile, titanium and zircon. Iluka acquired 18.3 percent of Metalysis in an effort to extract more value from its mined products.
Another promising company is Chilean miner White Mountain Titanium Corporation (OTCQB: WMTM), which is currently operating its Cerro Blanco Project, touted as one of the world's largest primary rutile and titanium deposits once it begins production. White Mountain expects to mine an estimated 112 million tonnes of rutile and is set to enter production status at the end of 2017.
The development of the new process of titanium production might be the key to unlocking the full potential of titanium. Once low-cost titanium has reached mass production stage, it can become a viable replacement for aluminum and stainless steel in everyday products, thanks to titanium's strength, light weight, and resistance to corrosion.
To contact the writer, email: v.hernandez@ibtimes.com.au