NZ Company Builds First 3D Printed Battery Powered Rocket Engine
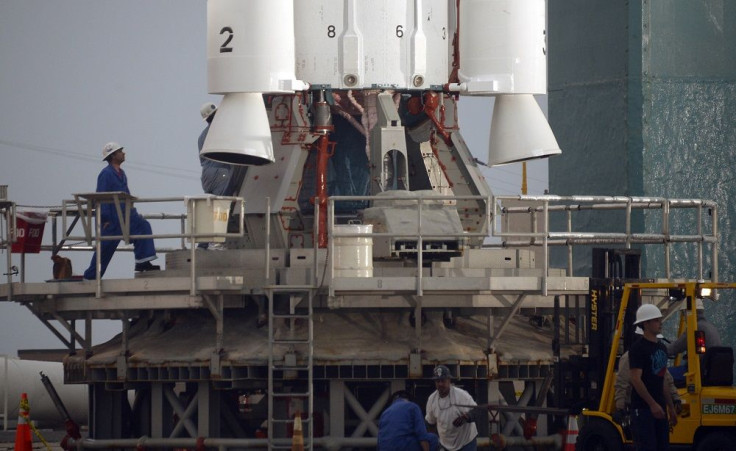
Another development in space exploration has been unlocked thanks to Rocket Lab, a New Zealand-based company that has built a 3D-printed titanium rocket engine with electric motors to drive turbopumps. Funding a space exploration costs hundreds of millions of dollars, but there’s a way to cut down on expenses now: 3D printing.
Rocket Lab has designed and built a lightweight satellite launcher called “Electron” and an engine called “Rutherford.” The products were unveiled in Colorado, USA, during the annual Space Symposium.
According to Rocket Lab, using their products will cut down space exploration costs up to 95 percent with the reduced amount of liquid fuel to be used. In perspective, the amount of fuel a satellite needs to orbit around the Earth is the same for a jetliner going from San Francisco to Los Angeles.
This is possible with the 4,600lbf turbopumps that inject the propellant into the engine. While the engine still runs on rocket fuel as propellant (liquid oxygen and refined kerosene), its turbopumps will be driven by brushless DC electric motors powered by lithium-polymer batteries. The engine will be placed in nine parts in the tail end of the rocket, and one will be located in its nose.
Rocket Lab added in a report by CNET that Rutherford is the first LOX-RP-1 engine to apply 3D printing for all its main components. The cooled thrust chamber, the injector, the pumps, and main propellant valves are all 3D printed, using titanium alloys through a technique called electron beam melting.
Aside from cutting down fuel costs, this process will curb the manufacturing process. According to leading space system company Lockheed Martin, a space rocket launch would averagely cost $225 million. In comparison, Rocket Lab’s Rutherford-equipped Electron launch is expected to cost around $4.9 million.
New Zealand is becoming quite known for 3D printing, with multiple aerospace companies allotting space for titanium 3D printing facilities. Tauranga’s Martin Aircraft recently welcomed its Chinese investors inside its facilities to show its titanium powder 3D printing technology. Layers and layers of titanium powder are fortified with lasers, forming desired airplane parts for manufacturing. One of the guests, Kuang Chi Science, or KCS, founder, Dr. Ruopeng Liu, expressed his optimism about the future of 3D printing in New Zealand.
“Manufacturing used to be about chopping away, but the technology here is all about adding – it’s a type of metamaterial. I think it’s the trend for the industry. We can see the potential that people can almost print anything,” said Liu in a post by China Topix.
Titanium plays a huge role in these advanced aerospace technologies, which means that the global demand for titanium will only increase as more companies adapt 3D printing. White Mountain Titanium (OCTQB: WMTM), a developing company in Cerro Blanco, Chile, is on its way to produce 112 million tonness of high-grade rutile. This kind of titanium production will secure companies all over the world with enough rutile to sustain additive processes needed to develop more technologies.
To contact the writer, email: v.hernandez@ibtimes.com.au